From our latest robotic arms like Sparrow and Cardinal, to our first autonomous mobile robot, Proteus, we’re excited to see the impact our technology is having in Amazon’s operations. We now have over 750,000 robots working collaboratively with our employees, taking on highly repetitive tasks and freeing employees up to better deliver for our customers.
With all of these efforts underway, it makes us particularly proud to share that we have just launched a new robotic system in time to help fulfill customer orders for holiday shopping this year. Sequoia is the name of this new technology, and it’s now operating at one of our fulfillment centers in Houston, Texas.
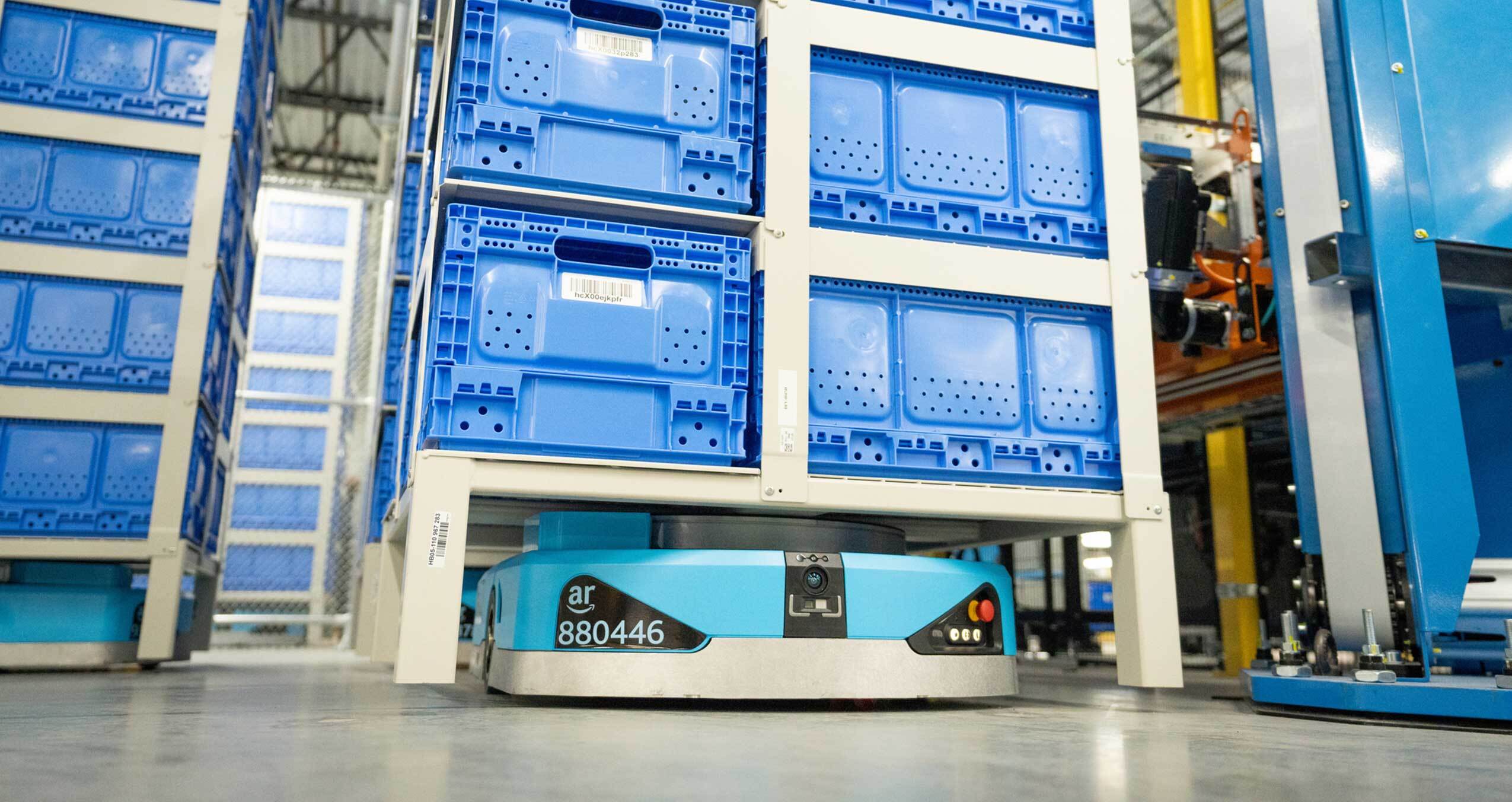
By reimagining how we store and manage inventory at our sites, Sequoia will help us delight customers with greater speed and increased accuracy for delivery estimates, while also improving employee safety at our facilities. Sequoia allows us to identify and store inventory we receive at our fulfillment centers up to 75% faster than we can today. This means we can list items for sale on Amazon.com more quickly, benefiting both sellers and customers. When orders are placed, Sequoia also reduces the time it takes to process an order through a fulfillment center by up to 25%, which improves our shipping predictability and increases the number of goods we can offer for Same-Day or Next-Day shipping.
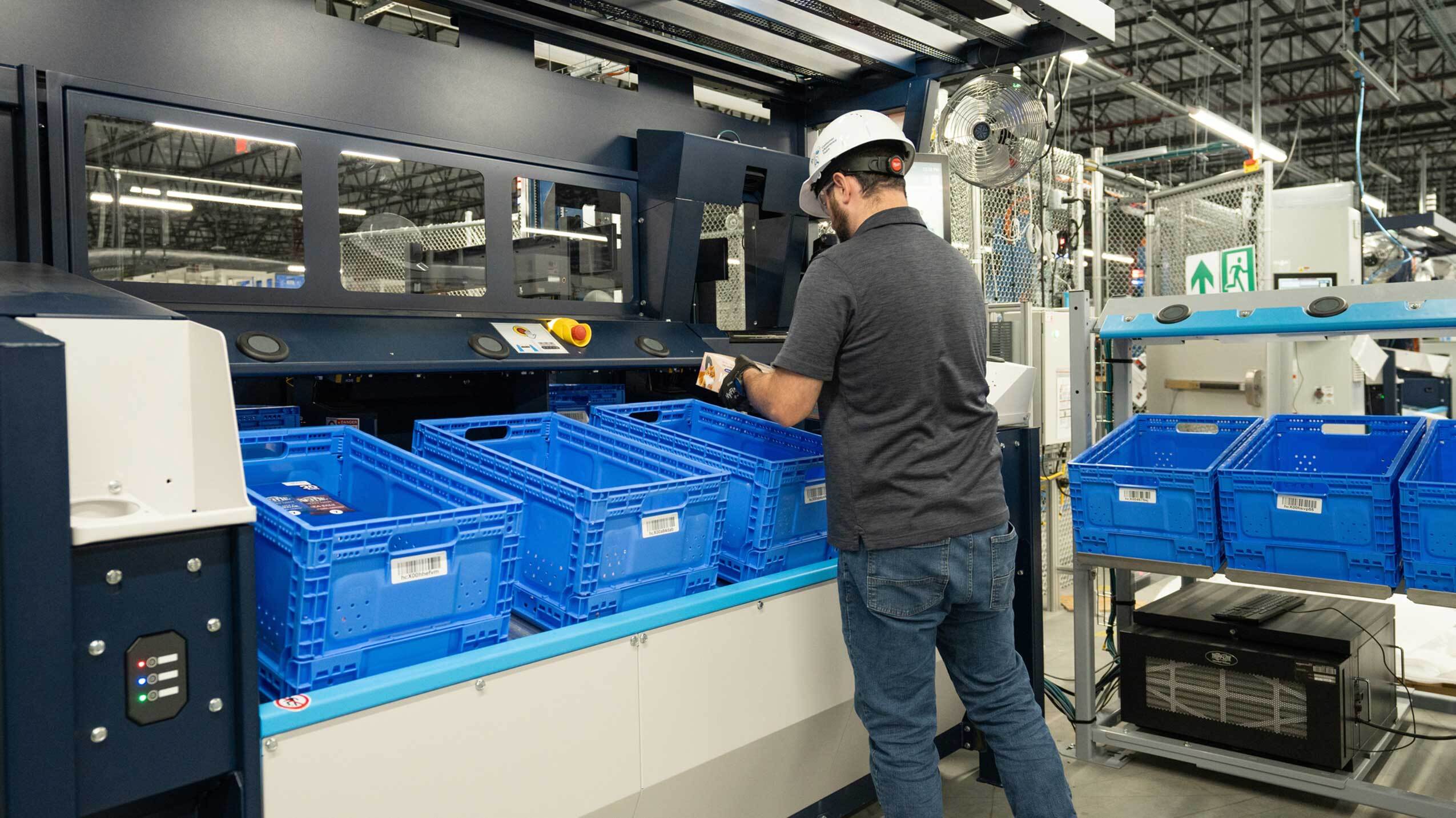
Building off a series of research and development efforts, Sequoia integrates multiple robot systems to containerize our inventory into totes, bringing together mobile robots, gantry systems, robotic arms, and a new ergonomic employee workstation. The system works by having mobile robots transport containerized inventory directly to a gantry, a tall frame with a platform supporting equipment that can either restock totes or send them to an employee to pick out inventory that customers have ordered.
These totes come to employees at a newly-designed ergonomic workstation that allows them to do all their work in their power zone, between mid-thigh and mid-chest height. With this system, employees will no longer have to regularly reach above their heads or squat down to pick customer orders, supporting our efforts to reduce the risk of injuries.
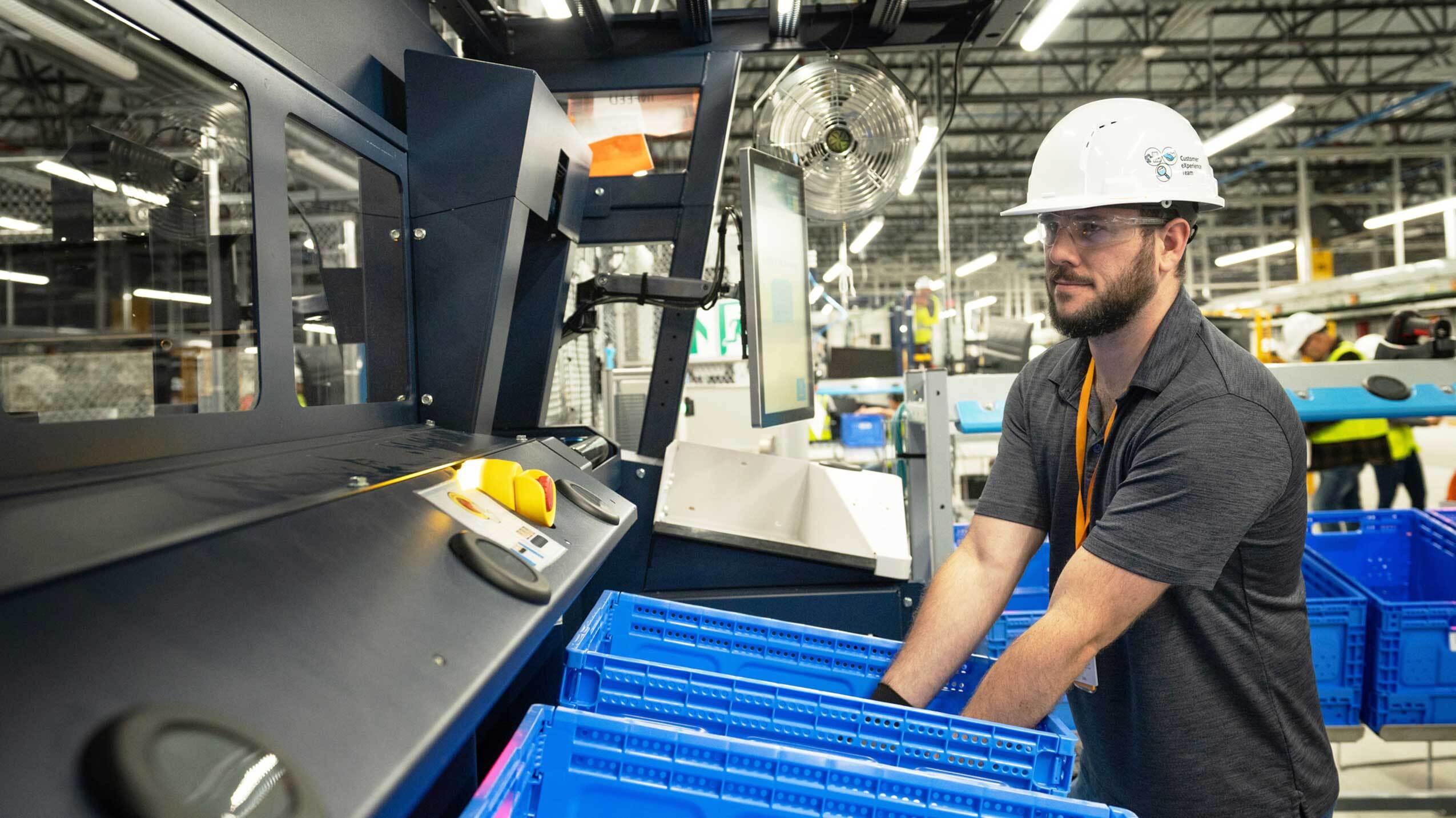
Once customer orders picked from inventory are retrieved, the remaining inventory needs to be consolidated so that our totes are full, and we are efficiently managing site storage. This is where our newest robotic arm, Sparrow, comes in, taking on the highly repetitive task of consolidating inventory in totes so that full totes can be returned to storage.
Working as a set of integrated robotics systems, Sequoia will dramatically simplify and optimize how we store goods and help employees pick those goods in a safe way. This feat comes thanks to the ingenuity of our technology teams as well as the partnership and regular feedback we get from operations employees about how we can use automation to make our workplace better. This collaboration is driving meaningful impact: Company data shows that, in 2022, recordable incident rates and lost-time incident rates were 15% and 18% lower, respectively, at Amazon Robotics sites than non-robotics sites. Sequoia will help continue this positive trend.
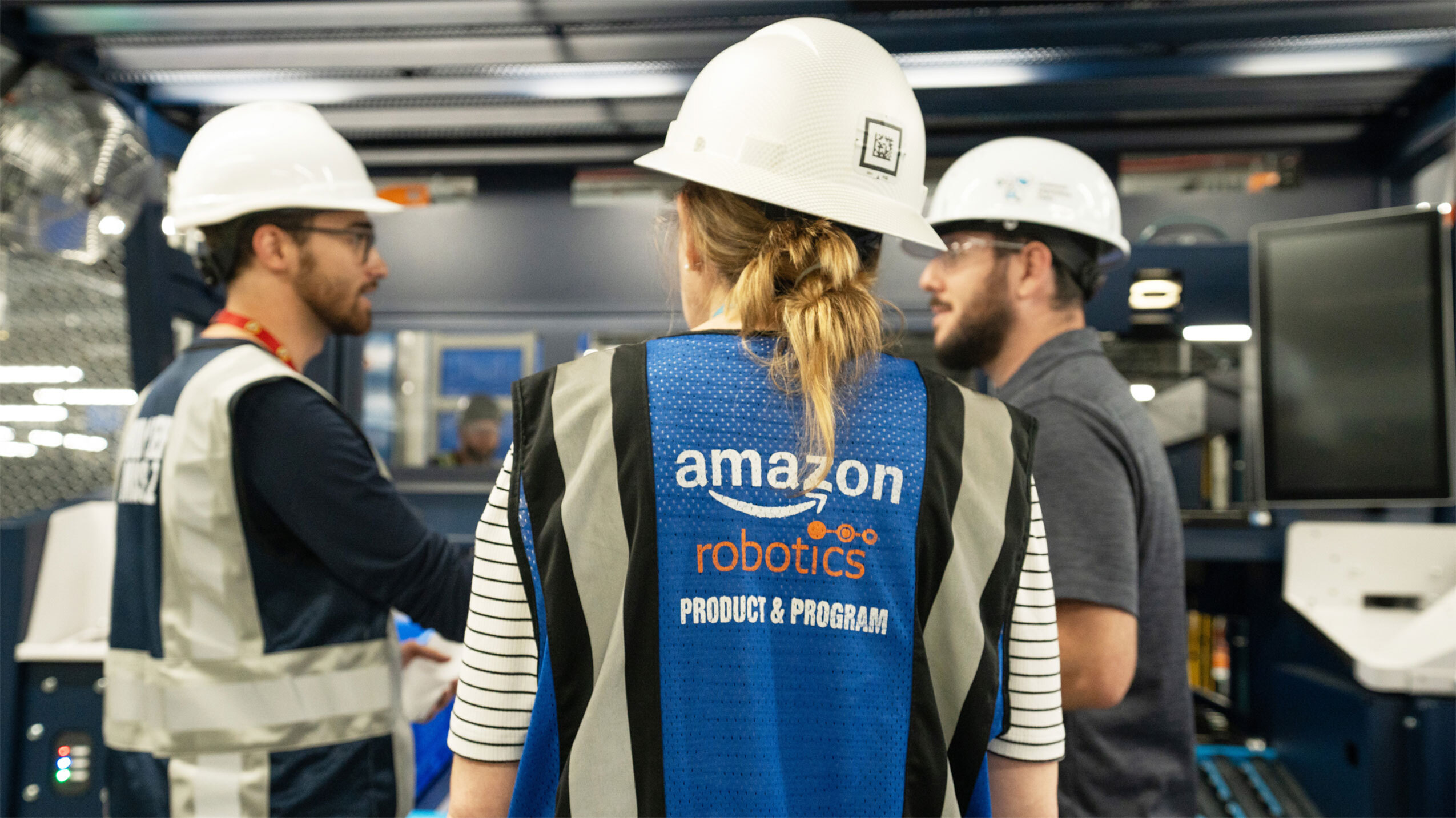
In addition to Sequoia, Amazon Robotics continues to invest in and try novel approaches to automation. That’s why we also have begun testing mobile manipulator solutions at our robotics research and development site just south of Seattle. These are mobile robots that can move while also grasping and handling items.
Broadening our partnership with Agility Robotics, we will begin testing their bipedal robot, Digit, for use in our operations. Agility is one of the companies Amazon invested in as part of the Amazon Industrial Innovation Fund. Digit can move, grasp, and handle items in spaces and corners of warehouses in novel ways. Its size and shape are well suited for buildings that are designed for humans, and we believe that there is a big opportunity to scale a mobile manipulator solution, such as Digit, which can work collaboratively with employees. Our initial use for this technology will be to help employees with tote recycling, a highly repetitive process of picking up and moving empty totes once inventory has been completely picked out of them.
Ensuring robotics are collaborative and support employees is central to how we design or deploy systems like Sequoia and Digit. Over the last 10 years, we’ve rolled out hundreds of thousands of robotics systems while also creating hundreds of thousands of new jobs within our operations. This includes 700 categories of new job types, in skilled roles, which didn’t exist within the company beforehand. By equipping our employees with new technology and training them to develop new skills, we’re creating career paths and new and exciting ways for people to contribute here at Amazon.
From the hardware to the artificial intelligence embedded in our robotics, we are passionate about technology that makes the work experience of our employees safer, easier, and less repetitive. Doing so gives our employees the time and opportunity to take a step back, look at how orders are moving though our sites, and find new ways to delight and serve our customers.
Trending news and stories
- A city in the palm of your hand: Exploring the intricate world of an Amazon Web Services chip
- How Amazon's delivery drones make smart landing decisions in unexpected conditions
- How to watch all the 'Conjuring’ movies on Prime Video
- Introducing Amazon Lens Live: Instant scanning, real-time product matches, and insights from Amazon's AI Shopping Assistant