When I was 19, I left college so I could come home to help support my family. I have seven siblings, and my dad was the family’s only supporter because my mom has lupus. I was looking for a good job, and luckily, my sister’s boyfriend told me about Amazon.
I started at Amazon in 2019 as a picker, which is the role responsible for retrieving items from shelves and packaging them for shipment to customers. To be honest, I was just here for a paycheck at first, but it turned into a lot more as I found new opportunities. Over the last three years, I’ve earned four promotions. I moved up fast, and I’m now an operations manager leading 80 employees at a fulfillment center in North Carolina.
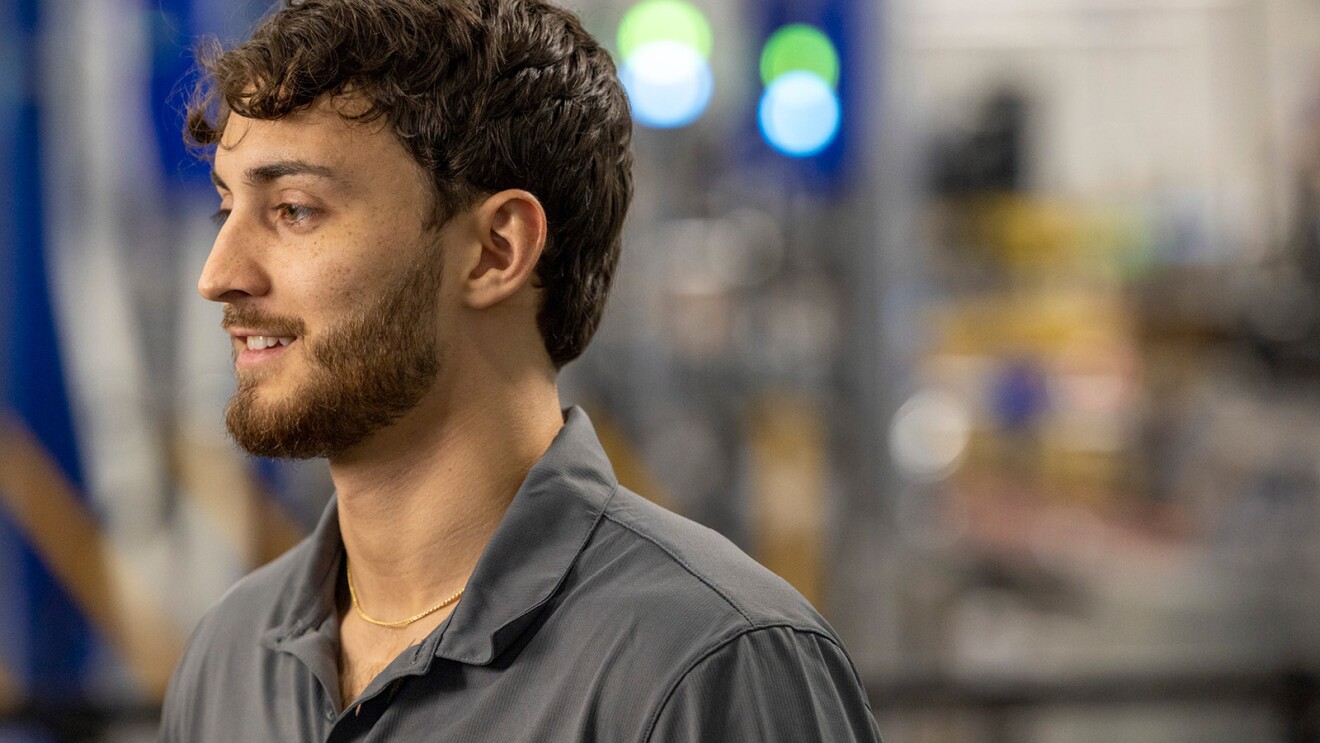
One of my favorite parts of the job is helping my team progress in their careers like I have. I've always been someone who loves to learn and ask questions, so meeting all these new people and learning about their backgrounds, their career goals, and who they are outside of work, is a joy in my life.
I also love being a part of the team that delivers what customers need when they need it. My friends and family are always asking me how in the world we deliver for customers the way we do. I even ordered a belt the day of a recent flight, and I got it two or three hours before I needed to get to the airport—that’s pretty incredible!
Improving operations while increasing employee safety presents the biggest challenge.
As I’ve worked my way up into a leadership role, one of the most challenging parts of my job has been figuring out how to constantly improve safety and production quality. It’s a big responsibility to keep employees safe while also helping them grow and improve. In an ideal world, I’d want all of my employees to progress to management roles one day, and new innovations from Amazon Robotics help them succeed in their roles.
One of our biggest helpers has been a robot called Hercules. The bot can lift more than 1,000 pounds, and it carries products across the fulfillment center so my employees don’t have to walk to retrieve products and move all of the orders. This is a huge help in improving our operations and safety, especially during busy times like the holidays. Our team recently retired our first Hercules robot; we all signed it and gave it a proper send off as a “thank you” for getting us through some of our busiest moments.
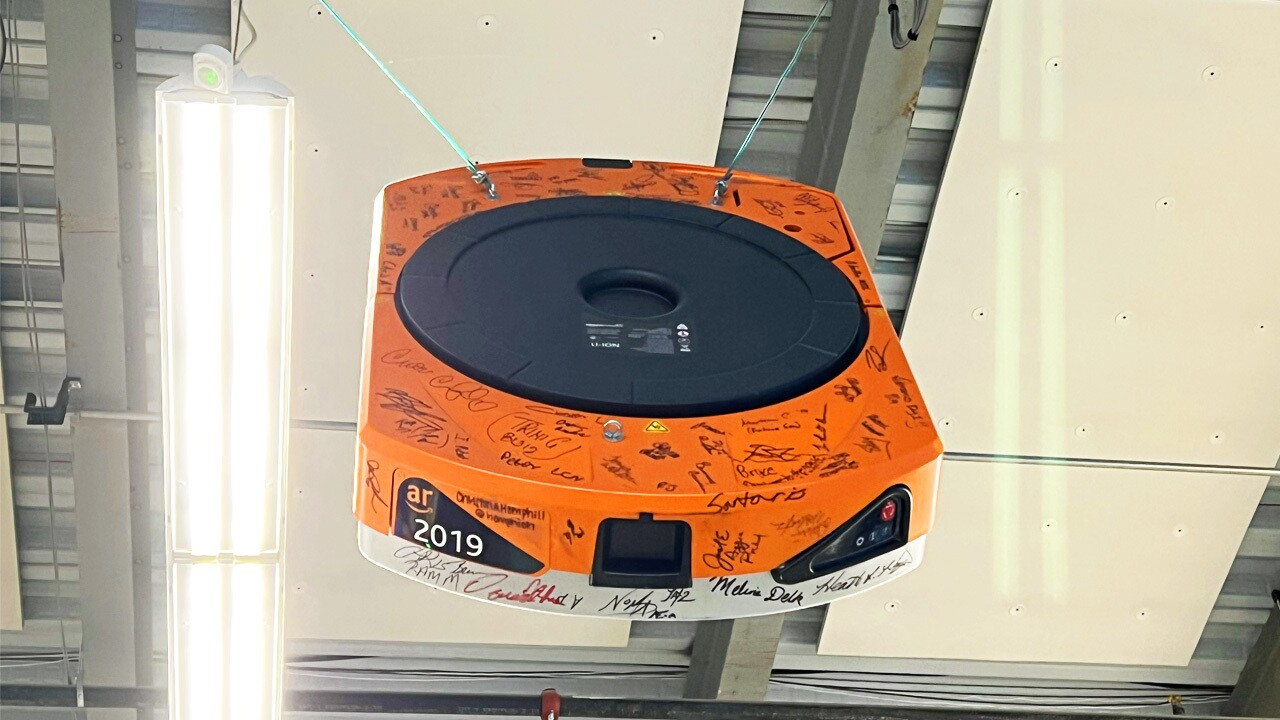
My team is really excited to see what’s coming next. Amazon recently announced two robots we’re particularly excited about. One of those is the new robot Proteus, which will be the first to roam freely outside restricted and fenced-off areas where our current robotic drive units operate. This means it will work alongside employees on new tasks in our facilities. For example, we currently have to move large and heavy carts that store packages in our outbound docks, and the Proteus robot will be able to help us do that.
01 / 03
We’re also really excited about Sparrow, another new robot that will help us handle items in inventory consolidation. We’re currently working with a similar robotic arm called Robin that is able to pick up packages, but Sparrow will be able to pick up individual products in inventory, and that will be a huge help to reduce repetitive work and free up time for my employees to focus on more engaging work.
01 / 02
Introducing new robots is a cool and important part of the job.
As we introduce new technology in our facility, two of the biggest focuses will be safety and training. We need to make sure employees know how to work with robots, and it’s also important that they understand exactly how the new technology can help them.
It’s really cool to be a part of training my employees to work alongside the new robots, and the Amazon Robotics team is super involved in making sure the technology is helping us deliver for customers. We have an engineer helping us out, and the vice president of Amazon Robotics, Joe Quinlivan, even comments on trouble tickets himself to stay involved in the process. We get a lot of support, and it’s exciting to see all these new things that will help us in our everyday lives.
Learn more about some of the new innovations powering Amazon’s delivery networks.
This essay from Sellers has been edited for length.
Trending news and stories
- Getting started with Alexa+: How to set up and personalize your experience
- How to watch ‘The Runarounds’ on Prime Video
- How to watch ‘Superman,’ directed by James Gunn, on Prime Video
- Amazon now offers same-day perishable grocery delivery in over 1,000 cities and towns with plans to double that reach by year's end